Clamping systems
Precise workpiece clamping made to measure.
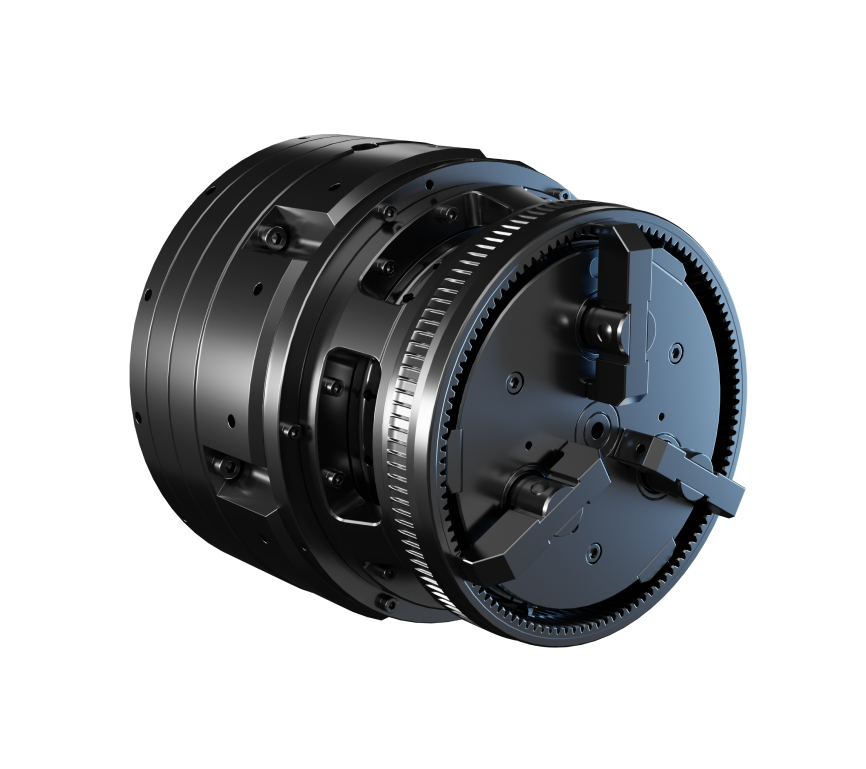
- Efficient and accurate centering < 0.01 mm
- Optimally adapted to difficult geometries and processes
- Guarantees the greatest possible tool freedom
- Smartly controlled and monitored
Workpiece clamping is the starting point for a successful machining process.
With stable lightweight construction, precise fine balancing and high process reliability, we guarantee sustainable, resource-efficient operation. This applies both to the machining process and to operator safety – naturally in compliance with the EC Machinery Directive 2006/42/EC.
We design, develop and manufacture our special clamping systems tailored to the individual geometry of your workpiece and the requirements of your machining process.
μ-THINKING®- for customized high-end production technology.
Here as a system for holding and machining ball screw nuts. Maximum repeat accuracy and very low wear. Highly automatable.
Here as a system with four individually controllable clamping levels for the mounting and flexible parting off of cylinder liners.
Here as a system for holding and complete machining of customised piston outer contours in a single clamping operation.
Here as a system with soft centring in the pitch circle of the toothing. Centrifugal force-independent and deformation-free clamping for external machining of deformation-critical components.
Here as a system for holding difficult workpieces with the option of simultaneous internal and external machining.
Here as a system with soft centring in the pitch circle of the toothing. Centrifugal force-independent and deformation-free clamping for internal machining of deformation-critical components.
Here as a system with two separate clamping levels for centring on different internal diameters with simultaneous optimum coaxial alignment.
Here as a system with positioning and oscillating compensating jaw clamping for holding and machining injection nozzles for the aerospace industry.
Here as a system with two clamping levels offset by 90°. Holding and processing of projecting shaft-shaped workpieces.
Here as a system with retractable workpiece fence for holding and complete machining of ring-shaped workpieces.
Here as a system for holding and machining workpieces in the rough machining process with integrated grip and pull-down function.
Here as a system for the passive centring of differential housings with process-safe plane clamping.
Here as a system with active centring and face clamping of electric motors. With additional centrifugal force-controlled elements for sealing the workpiece during machining.
Here as a system for compact internal clamping. Centrifugal force-independent and deformation-free clamping for external machining of thin-walled workpieces.
Highly dynamic system in compact design. Centrifugal force-independent and deformation-free clamping here for holding and machining thin-walled cams.
Here as a system with pre-centring, positioning and subsequent face clamping for holding and machining complex levers.
Here as a system with soft centring in the pitch circle of the toothing. Centrifugal force-independent and deformation-free clamping for internal machining of deformation-critical components.
Here as a system with active eccentric centring to the centre of rotation for holding and machining turbine housings.
Here as a system for turning and drilling thin-walled aluminium housings with active vibration damping.
Here as a system with active damping for the mounting and vibration-free processing of high-quality enclosures.
Here as a system with vacuum clamping for processing hip joints in two positions; with integrated centrifugal force compensation.
Here as a system for holding and processing medical devices.Few moving parts, maximum repeat accuracy and very low wear.
Here as a system in a sealed and stainless design for holding housing components in an industrial cleaning process.
Here as a system for holding wheels in a measuring and balancing process. Designed with a large radial stroke and maximum precision over the entire clamping range.
Here as a system for holding X-ray discs in a balancing process.
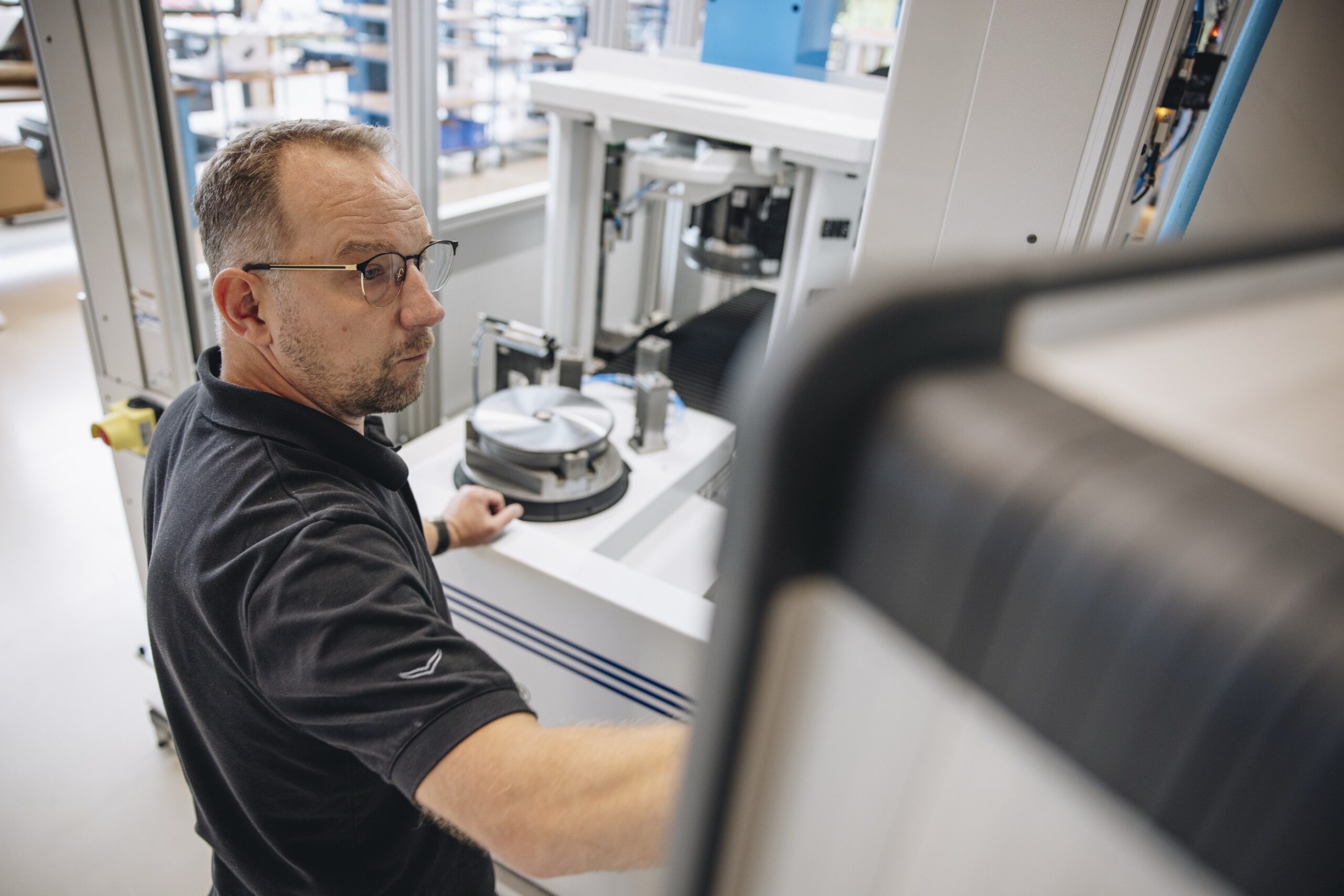
Highest quality thanks to strict controls.
We offer you high-end quality because our systems undergo two tests during manufacture and before delivery:
- Measurement of each relevant individual part before assembly: checking dimensional accuracy, shape and position tolerances.
- Extensive endurance tests on our test bench after assembly.
Everything from a single partner.
For new machines as well as for conversion projects: We accompany you from the first idea and the initial technical concept through design, production and project management to commissioning and far beyond.
“We inventors from the Black Forest have always had a high technological influence on progress within many industries – worldwide. Our high level of specialization is a guarantee for both technical challenges and sustainable business – and therefore future security.”
Johannes Sterman, Managing Director